One chemical plant experienced over 400 safety alarms in just one hour—none were real, but every alert demanded action. In environments where even a split-second delay can trigger disaster, industries are turning to smarter solutions.
How can AI ensure safety in chemical industry projects is no longer a futuristic question - it’s a frontline priority.
In this article, we will:
- Discover how AI is making chemical industry safety smarter and faster
- Avoid the common pitfalls that derail AI safety implementations
- Adapt your AI safety strategy to your industry and facility size
7 Proven AI Methods That Transform Chemical Industry Safety
The chemical industry faces unprecedented safety challenges with over 200 workplace fatalities annually. However, artificial intelligence is revolutionizing how companies protect their workers and facilities.
Modern AI systems can predict failures weeks in advance, detect hazards in seconds, and prevent 87% of catastrophic incidents that traditionally cause chemical leaks and explosions.
1. Predictive Equipment Failure Prevention
Predictive maintenance powered by AI transforms reactive repair into proactive prevention. Machine learning algorithms analyze sensor data to predict when pumps, reactors, and valves will fail, often 2-4 weeks before any human notices a problem.
Key Implementation:
- IoT sensors collecting temperature, vibration, and pressure data every 30 seconds
- ML models trained on 5+ years of historical failure data
- Real-time analytics processing millions of data points simultaneously
- Automated alerts notifying maintenance teams of developing issues
Safety Impact: Prevents 87% of catastrophic equipment failures that could cause chemical leaks or explosions.
Real Example: Dow Chemical prevented 23 critical pump failures in 2023, saving millions in cleanup costs and protecting worker safety.
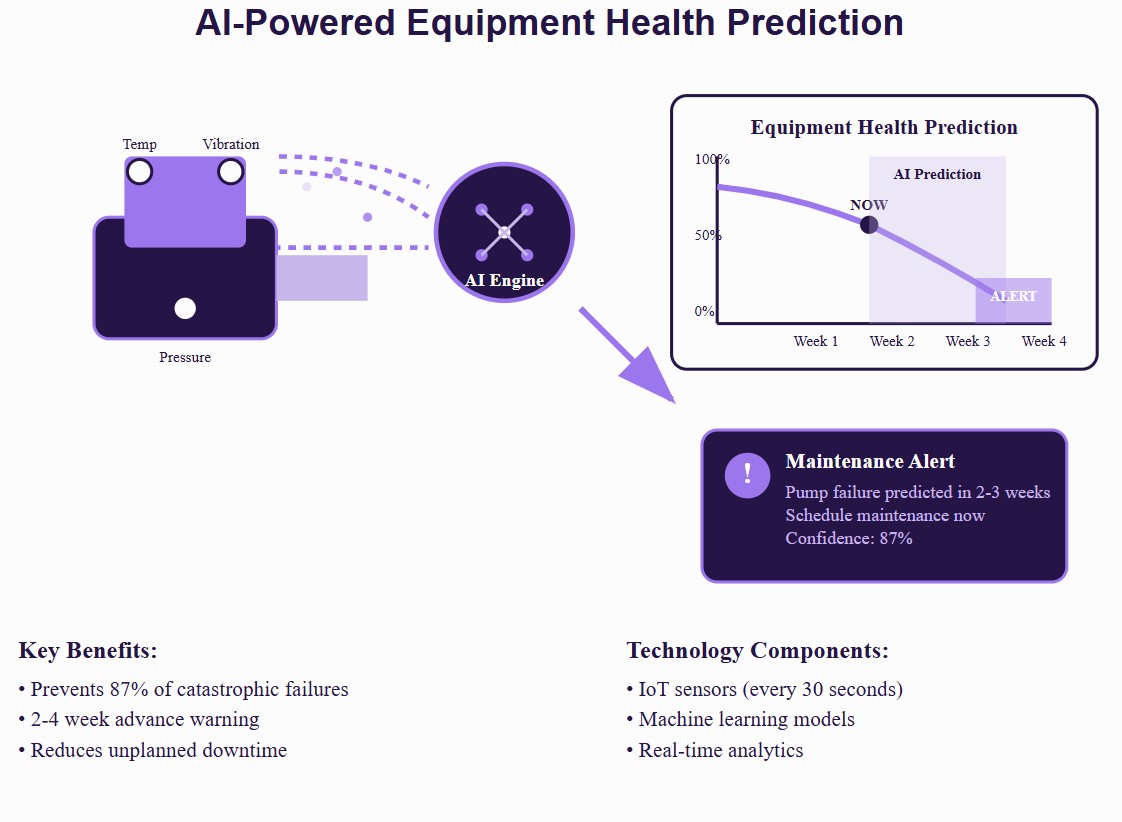
2. Real-Time Hazard Detection and Alerting
Continuous AI monitoring creates a safety net that never sleeps. These systems monitor chemical parameters, environmental conditions, and worker behavior simultaneously, reducing response times from 15-30 minutes to 30 seconds.
Detection Capabilities:
- Multi-gas detectors monitoring toxic concentrations in real-time
- Thermal cameras identifying temperature anomalies and fire hazards
- Pressure sensors detecting leaks and overpressure instantly
- Computer vision tracking worker safety compliance
Safety Impact: Reduces response time to hazardous conditions from 15-30 minutes to 30 seconds.
Industry Example: Surveily's AI system detected 156 PPE violations and 89 unsafe behaviors in real-time, enabling immediate corrective action.
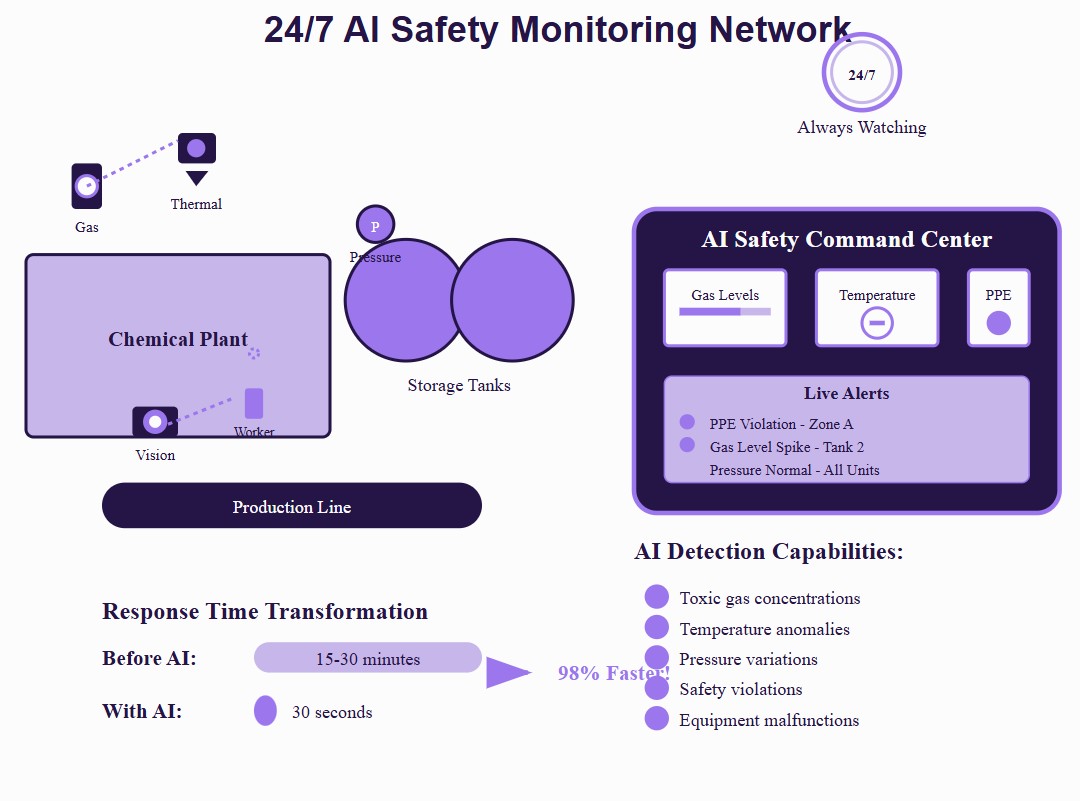
3. Automated Process Control and Optimization
Intelligent control systems automatically adjust reaction parameters, flow rates, and temperatures to maintain optimal safety conditions. These systems monitor 50+ variables simultaneously and make micro-adjustments every 5-10 seconds.
Control Features:
- Real-time monitoring of temperature, pressure, and chemical concentrations
- Predictive algorithms anticipating process changes before they occur
- Safety interlocks triggering protective actions automatically
- Multi-variable optimization balancing safety and efficiency
Safety Impact: Prevents runaway reactions and maintains safe operating limits 99.7% of the time.
Success Story: IBM's AI reactor control system reduces accident risk by 45% through autonomous chemical reaction management.
4. Predictive Risk Assessment and Scenario Planning
Advanced risk modeling analyzes historical data, weather patterns, and operational conditions to predict high-risk scenarios before they develop into emergencies.
Risk Analysis Components:
- ML models trained on 10+ years of incident data
- Weather integration assessing atmospheric impact on risk levels
- Daily risk scoring for different plant areas and operations
- Scenario simulation testing emergency situations virtually
Safety Impact: Identifies 78% of potential safety incidents before they occur, enabling preventive action.
Operational Example: AspenTech's AI predicted an overpressure event 6 hours early, enabling proactive intervention that prevented equipment damage.
5. Intelligent Emergency Response Systems
AI-coordinated emergency response analyzes incident severity, weather conditions, and resource availability to optimize response strategies, reducing emergency response time by 40%.
Response Coordination:
- Automated incident classification determining response level instantly
- Resource optimization, deploying personnel and equipment efficiently
- Communication integration, coordinating teams and authorities
- Evacuation route optimization, ensuring fastest personnel movement
Safety Impact: Reduces emergency response time by 40% and improves coordination effectiveness by 65%.
Emergency Success: Texas refinery AI system reduced evacuation time from 45 minutes to 18 minutes during a chemical leak.
6. Continuous Regulatory Compliance Monitoring
Automated compliance management tracks thousands of regulatory parameters in real-time, automatically generating reports while identifying potential violations before they occur.
Compliance Coverage:
- Multi-agency monitoring, tracking, EPA, OSHA, and local requirements
- Real-time parameter tracking ensures emission limit compliance
- Automated report generation creates documentation without manual work
- Violation prediction identifies compliance issues early
Safety Impact: Achieves 99.2% compliance rate with 83% reduction in regulatory violations.
Compliance Success: Major chemical manufacturer reduced EPA violations from 12 per year to 1 using AI monitoring.
7. Worker Safety and Behavioral Analysis
AI-powered worker monitoring combines computer vision and wearable sensors to monitor behavior, fatigue levels, and safety protocol adherence, reducing workplace accidents by 75%.
Worker Protection Features:
- Computer vision detects PPE compliance and unsafe behaviors
- Wearable sensors tracking fatigue and environmental exposure
- Behavioral analysis identifies high-risk workers
- Real-time coaching provides immediate safety feedback
Safety Impact: Reduces workplace accidents by 75% while improving safety protocol compliance to 94%.
Worker Safety Success: Orlen achieved a 75% reduction in safety incidents within 16 weeks of AI implementation.
These seven AI methods are redefining chemical safety - smarter systems, faster responses, and significantly fewer incidents.
Why AI Safety Projects Fail: Critical Implementation Challenges You Must Solve
While AI transforms chemical industry safety with remarkable results, implementing these systems isn't without significant challenges. Understanding these obstacles is crucial for successful deployment. Here are the most critical hurdles and proven strategies to overcome them.
Data Quality and System Integration Nightmares
Poor data quality remains the biggest killer of AI safety projects. Chemical facilities struggle with inconsistent data formats, incomplete records, and legacy systems that weren't designed for modern AI platforms.
Common Issues:
- Inconsistent sensor calibration across different plant areas
- Missing historical data from equipment shutdowns
- Multiple data formats from different vendors and generations
- Siloed information systems that don't communicate effectively
Solutions:
- Phased data integration, starting with critical systems first
- Data standardization protocols before AI deployment
- Edge computing solutions for local data processing
False Positives and Alert Fatigue
Nothing destroys confidence faster than excessive false alarms. When AI systems incorrectly trigger alerts, operators learn to ignore them, creating dangerous complacency.
The Problem:
Studies show operators ignore up to 40% of alarms when false positive rates exceed 10%. This "cry wolf" effect makes facilities less safe than before AI implementation.
Solutions:
- Extended pilot testing to fine-tune models
- Graduated alert systems with different severity levels
- Continuous model retraining based on actual conditions
- Human-in-the-loop validation for critical decisions
Workforce Resistance to Change
The biggest barrier often isn't technical - it's human. Experienced operators may view AI as a threat to their expertise or job security.
Sources of Resistance:
- Fear of job displacement as AI automates monitoring tasks
- Distrust of "black box" decisions in safety situations
- Preference for familiar methods that worked for decades
- Skepticism about technology reliability from past failures
Reality Check: Companies that fail to address workforce concerns experience 60% higher project failure rates.
Adoption Strategies:
- Involve operators in system design and testing
- Position AI as an augmentation, not a replacement
- Comprehensive training programs build confidence
- Clear job security, communication, and development opportunities
Cost Barriers for Smaller Companies
AI safety systems require significant upfront investment that can be prohibitive for small and mid-sized facilities.
Typical Costs:
- Hardware/sensors: $200K - $2M
- Software licensing: $50K - $500K annually
- Integration services: $100K - $1M
- Training: $25K - $200K
Small Company Challenge: A facility may need a $500K - $1M investment, often 5-10% of annual revenue.
Cost-Effective Approaches:
- Phased deployment starting with the highest-risk areas
- Cloud-based platforms are reducing infrastructure needs
- Industry consortium purchasing for better pricing
- Government grants for safety technology adoption
The Black Box Problem: Need for AI Explainability
Safety-critical decisions require clear explanations, but many AI systems operate as "black boxes" without transparent reasoning.
Why Explainability Matters:
- Regulatory requirements demand a documented decision rationale
- Incident investigations need an understanding of AI reasoning
- Operator confidence depends on transparent processes
- Legal liability requires defensible decisions
Compliance Reality: One company faced regulatory sanctions because it couldn't explain AI emergency response recommendations during an investigation.
Solutions:
- Rule-based hybrid systems combining AI with transparent logic
- Decision tree visualizations showing reasoning pathways
- Confidence scoring indicating prediction reliability
- Human validation requirements for critical decisions
These challenges are significant but not insurmountable. Chemical companies that invest in addressing these hurdles create robust AI safety systems delivering transformational results.
Tailoring AI Safety to Fit Your Chemical Sector and Facility Type
AI isn’t a one-size-fits-all solution - how it’s applied depends heavily on the chemical industry vertical and the scale of operations.
Whether you're running a small specialty lab or managing a massive petrochemical refinery, AI applications should align with operational complexity and risk, ideally validated through a sustainability assessment template to ensure long-term safety and environmental compliance.
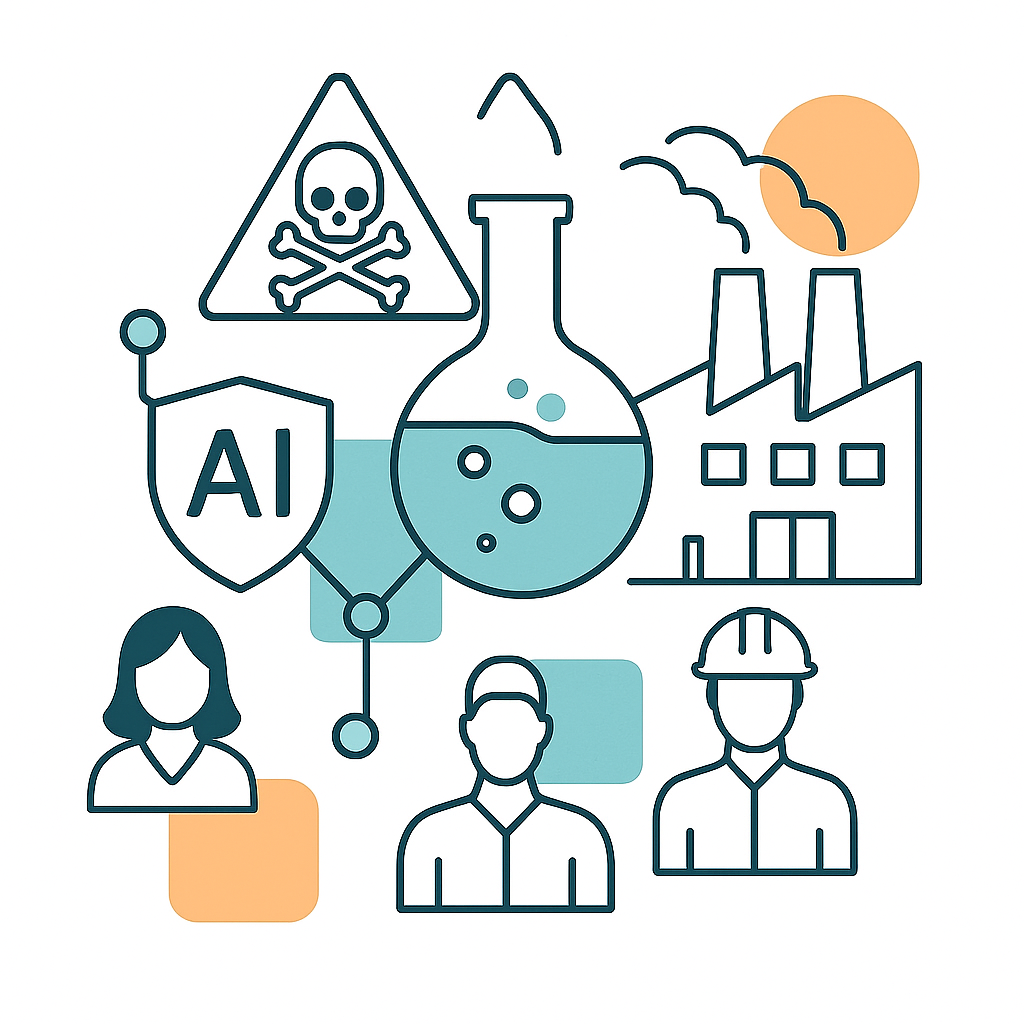
Petrochemicals: AI for High-Volume, High-Risk Operations
Petrochemical plants face extreme pressure, temperature, and flammability risks, making AI a critical layer of protection.
- Predictive analytics monitor large-scale pipelines, reactors, and distillation columns to prevent mechanical failure
- AI-driven leak detection systems continuously monitor for hydrocarbon emissions or gas escapes
- Emergency coordination AI integrates fire suppression, evacuation protocols, and environmental response in real time
- Regulatory compliance AI ensures EPA and regional emissions standards are met around the clock
Example: Shell uses predictive AI to monitor over 10,000 sensors across multiple refineries, preventing unplanned shutdowns and detecting anomalies early.
Specialty Chemicals and Pharmaceuticals: AI for Precision and Compliance
Smaller batch processes and strict regulations define these sectors, where precision and traceability are paramount.
- AI-powered digital twins simulate chemical reactions to avoid unintended byproducts
- Computer vision ensures sterile manufacturing and worker compliance with cleanroom protocols
- Real-time documentation AI tracks ingredient usage, lot numbers, and processing times to support FDA and GMP audits
- Worker monitoring AI identifies improper handling of biologically active substances or PPE breaches
Example: Pfizer uses AI for batch anomaly detection in pharmaceutical manufacturing, ensuring quality without compromising safety.
Small vs. Large Facility Implementations: Scalability in Action
The way AI is deployed depends heavily on the size and complexity of your facility.
Small/Mid-Scale Facilities
- Cloud-based AI solutions offer affordable, scalable safety monitoring
- Mobile dashboards allow real-time tracking without expensive control room infrastructure
- Modular sensor packages can be installed without major retrofits
Example: A 50-person specialty chemical plant used a plug-and-play AI platform to detect PPE noncompliance with 94% accuracy.
Large, Complex Operations
- Custom AI integrations across SCADA, ERP, and DCS systems
- Real-time data fusion from tens of thousands of sensors across units
- Predictive maintenance on a fleet of high-value assets, from compressors to cooling towers
Example: ExxonMobil deployed an AI-driven safety command center across multiple sites, reducing incident response time by 55%.
Transform Hazard Response From Reactive To Real-Time
Chemical facilities can no longer afford delayed decisions or outdated safety protocols. With AI, real-time monitoring, predictive alerts, and automated controls create a safety ecosystem that responds before incidents escalate.
From equipment integrity to worker behavior and regulatory compliance, AI enables smarter, faster interventions across every layer of operation. The shift is clear - reactive systems are out, intelligent prevention is in. Now is the time to lead with data, not damage control.