Think managing one project is hard? Try juggling over 30,000 parts, global regulations, and software updates - all in a single car. That’s the daily reality behind how the automotive industry approaches project management.
From digital twins to AI-powered dashboards, this high-stakes world blends engineering precision with fast-paced innovation in ways most industries can’t imagine.
In this article, we will:
- Master the strategies driving today’s most successful automotive projects
- See how bold project decisions led to industry-changing wins
- Use the right tools to manage every stage of automotive development
7 Strategic Approaches That Transform Automotive Project Delivery
The automotive industry manages some of the world's most complex projects - coordinating 30,000+ components, global supply chains, and strict regulatory requirements while racing to meet market launch deadlines.
Here's exactly how leading automotive companies master this complexity through seven proven strategic approaches.
1. Hybrid Methodologies: Combining Speed with Precision
Modern automotive companies don't rely on a single project management approach - they strategically blend methodologies to match the unique demands of different project components.
Key Implementation Strategies:
- Stage-Gate for Hardware: Use structured phases (Concept → Design → Testing → Production → Launch) for physical components requiring extensive validation and long lead times
- Agile for Software: Deploy rapid development sprints for in-vehicle software, infotainment systems, and over-the-air update capabilities
- Integration Points: Create specific checkpoints where hardware and software development cycles synchronize for seamless integration
- Flexibility by Project Type: EV startups like Tesla emphasize Agile throughout, while legacy OEMs like Ford blend both approaches based on component complexity
This dual-methodology approach enables automotive companies to maintain safety and quality standards for critical hardware while achieving the rapid innovation cycles necessary for competitive software features.
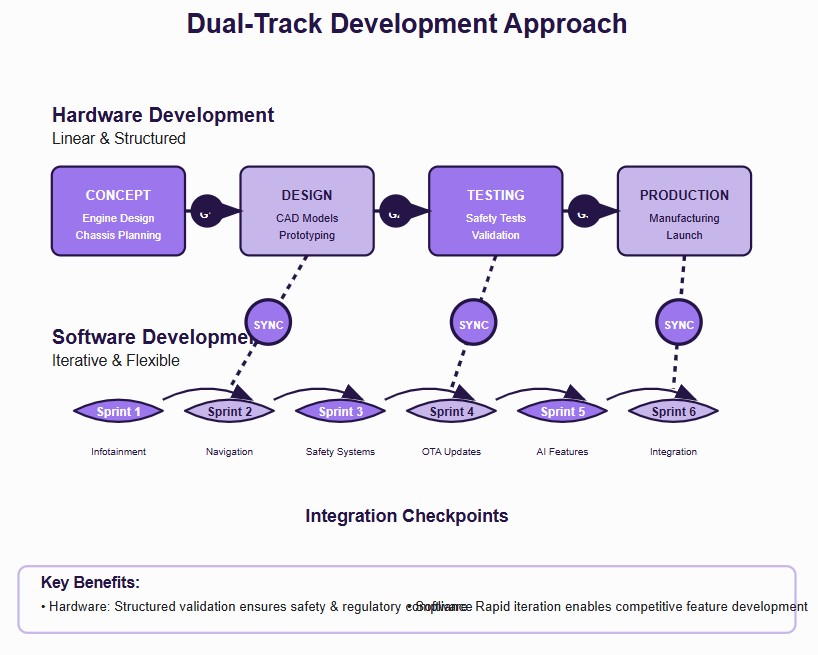
2. Integrated Cross-Functional Teams: Breaking Silos from Day One
Successful automotive projects eliminate departmental handoffs by creating fully integrated teams where all disciplines work in parallel from project inception.
Core Team Integration Elements:
- Concurrent Engineering: Design, manufacturing, procurement, and compliance teams collaborate simultaneously rather than sequentially
- Early Supplier Involvement: Key Tier 1 suppliers join development teams during initial design phases to ensure manufacturability and cost optimization
- Shared Accountability: All team members have joint responsibility for project success rather than individual departmental goals
- Co-location Strategy: Physical or virtual project spaces where cross-functional teams maintain constant communication and rapid decision-making
Companies like BMW and Mercedes-Benz have perfected this collaborative model, reducing development time by up to 30% while improving quality through early issue identification and resolution.
3. Platform-Based Development: Maximizing Resource Efficiency
Platform-based development transforms project economics by creating shared architectural foundations that support multiple vehicle variants, enabling extraordinary resource optimization.
Strategic Platform Benefits:
- Parallel Development: Multiple vehicle models can be developed simultaneously using shared engineering resources and proven component designs
- Cost Reduction: Standardized components achieve economies of scale while reducing tooling and development investments per vehicle
- Risk Mitigation: Proven platform elements reduce technical risk for new vehicle programs built on established foundations
- Global Scalability: Single platforms can support region-specific variants while maintaining manufacturing consistency across markets
Volkswagen's MQB platform supports over 40 vehicle models, from compact cars to large SUVs, demonstrating how platform strategies enable massive project portfolio efficiency without compromising individual vehicle character.
4. Lean Manufacturing Principles: Eliminating Waste at Every Level
Lean principles, pioneered by Toyota, extend far beyond manufacturing into comprehensive project management philosophies that eliminate inefficiency throughout development processes.
Essential Lean Project Applications:
- Value Stream Mapping: Identify and eliminate non-value-adding activities in development workflows, from unnecessary approvals to redundant documentation
- Just-in-Time Coordination: Synchronize development activities so resources, decisions, and deliverables arrive precisely when needed
- Continuous Improvement (Kaizen): Regular process reviews and refinements to eliminate bottlenecks and improve team efficiency
- Mistake-Proofing (Poka-Yoke): Build quality checks into every development stage to prevent defects from progressing to later phases
This obsession with efficiency enables automotive companies to manage extraordinary complexity while maintaining competitive development costs and accelerated time-to-market performance.
5. Program-Level Oversight: The Chief Engineer Model
Automotive projects require sustained leadership across multi-year development cycles, leading to the evolution of the Chief Engineer model, where senior leaders take comprehensive program ownership.
Chief Engineer Authority Structure:
- End-to-End Responsibility: Complete accountability from initial concept through production launch and market performance
- Cross-Functional Leadership: Direct authority over design, engineering, manufacturing, procurement, and marketing teams
- Technical Decision Rights: Final authority on complex technical trade-offs affecting performance, cost, and timeline
- Budget Ownership: Complete financial responsibility for program profitability and resource allocation decisions
Honda and Nissan have refined this model over decades, creating program leaders who combine deep technical expertise with business acumen, ensuring consistent decision-making throughout extended development cycles.
6. Tech-Driven Planning: Digital Tools for Complex Coordination
Modern automotive project management leverages sophisticated digital ecosystems to coordinate vast complexity and enable real-time decision-making across global teams.
Critical Technology Applications:
- PLM Systems: Centralized platforms managing design data, engineering changes, supplier collaboration, and regulatory compliance across thousands of components
- Digital Twins: Virtual prototyping and testing capabilities that reduce physical prototype costs while accelerating validation cycles
- AI-Powered Analytics: Predictive algorithms that identify potential delays, optimize resource allocation, and track critical KPIs like time-to-market and quality metrics
- Real-Time Dashboards: Integrated visibility platforms providing instant project status updates across all development streams and global locations
Ford and General Motors are investing heavily in these digital capabilities, recognizing that data-driven project management provides decisive competitive advantages in development speed and quality.
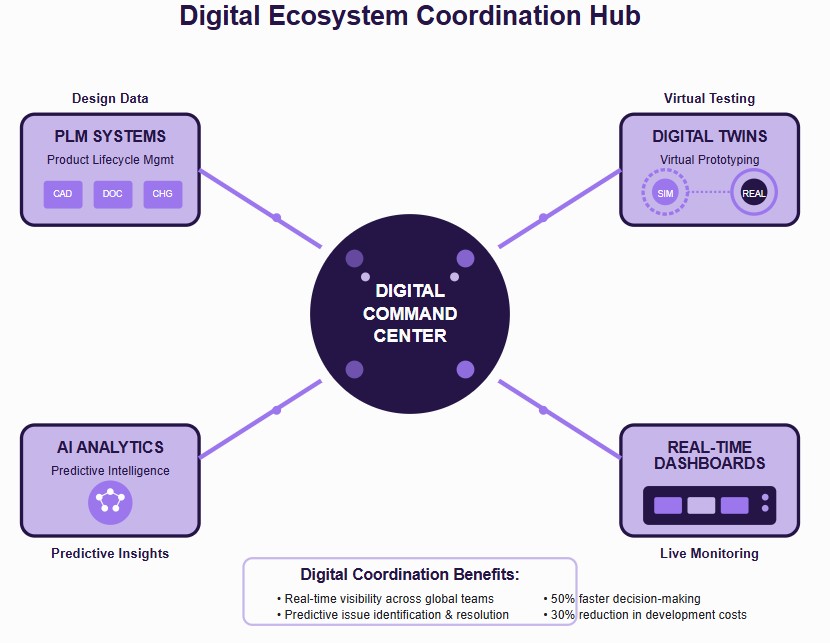
7. Global PMOs and Standardization: Consistency Across Complexity
Large automotive manufacturers establish global Project Management Offices to ensure consistent processes, quality standards, and regulatory compliance across worldwide operations.
Global PMO Capabilities:
- Standardized Methodologies: Unified project management processes, tools, and templates that enable seamless collaboration across regions
- Compliance Management: Centralized oversight ensuring adherence to safety, environmental, and quality standards across all markets
- Knowledge Transfer: Systematic capture and sharing of lessons learned, best practices, and technical innovations across global teams
- Resource Optimization: Coordinated allocation of specialized expertise and capabilities across multiple concurrent programs
This combination of global standardization with regional flexibility enables companies like Volkswagen Group and Toyota to develop vehicles efficiently for diverse international markets while maintaining consistent quality and compliance standards.
These seven strategic approaches represent decades of evolution in managing the world's most complex industrial projects. As vehicles become increasingly software-defined and globally connected, these proven methodologies continue evolving, setting new standards for complex project coordination across all industries.
Breakthrough Project Victories: When Automotive Giants Overcame Impossible Odds
These real-world case studies highlight how leading automakers like Tesla, Toyota, and Ford used project management to overcome major challenges and deliver industry-shaping results.
Tesla Model 3 Production Ramp: Agile Manufacturing Unleashed
Problem:
In mid‑2017, Tesla hit a wall during the Model 3 launch—production rates were stagnating at a few hundred cars per week. Severe quality issues arose due to rushed welding and unrefined assembly processes
Solution:
Tesla implemented “agile manufacturing” on the factory floor:
- The line was paused whenever defects were identified
- Rapid iteration sprints were used to troubleshoot welding, tooling, and layout
- They embraced real-time feedback loops, making adjustments within days
Outcome:
- Tesla increased production to ~1,000 vehicles/week by March 2018 and reached ~2,000/week shortly after
- By June 2018, they shipped ~5,000 Model 3s in a single week, just hours behind Musk’s aggressive year-end target
Results:
- Tesla transformed from “production hell” to a scaled manufacturing operation
- Achieved 5,000/week within ~18 months of ramp-up - rapid for automotive standards
- Demonstrated that Agile methodology can drive high-volume hardware production
Toyota Prius Hybrid Rollout: Platform-Driven Project Success
Problem:
Launching the Prius in the 1990s posed massive challenges: unproven hybrid tech needed to be integrated into existing manufacturing lines at scale, without exploding costs or slowing production
Solution:
- Toyota used a platform strategy, integrating the Prius hybrid system into its standard assembly lines at multiple plants (e.g., Takaoka, Tsutsumi)
- Employed concurrent engineering and lean production, ensuring supply chain, design, and processes aligned early on
Outcome:
- Achieved one Prius off the line every minute, compared to 8–10 minutes previously
- Sold over 100,000 units in the first three years, with hybrid tech reaching 15 million units worldwide across models
Results:
- Mass-market adoption of hybrids
- Proved platform integration and lean manufacturing can drive cost-effective innovation
- Established Toyota as a hybrid pioneer, with a continuous hybrid rollout dominating their product line
Ford F‑150 Lightning: Digital-Focused Electric Pickup Launch
Problem:
Ford faced a major transformation: adapting its iconic F‑150 for the software-defined EV era. This required embedding advanced connected features, cloud integration, and digital manufacturing - all while retaining legacy build standards.
Solution:
- Adopted a cloud-first, data-driven project management approach
- Digitized factory operations with screen-based instructions and autonomous vehicles (e.g., "skillets") on the line.
- Integrated software, engineering, and procurement teams in early planning
Outcome:
- Launched in 2022, with critical acclaim for connected features and EV-range performance
- Production centered at a new EV-optimized Rouge facility, streamlining operations using digital systems
Results:
- Positioned Ford as a software-defined vehicle manufacturer
- Earned strong market adoption and credibility in the EV truck segment
- Demonstrated that digital project management can transform legacy automakers into tech-forward leaders
Automotive PM Tech Stack: Tools That Drive Execution from Concept to Launch
Managing complex vehicle programs across geographies, disciplines, and timelines requires more than strategy - it demands the right digital tools. Leading automakers rely on a powerful ecosystem of platforms to stay aligned, agile, and audit-ready at every stage of development.
Below are the key categories of project management tools used across the industry and how each contributes to project success.
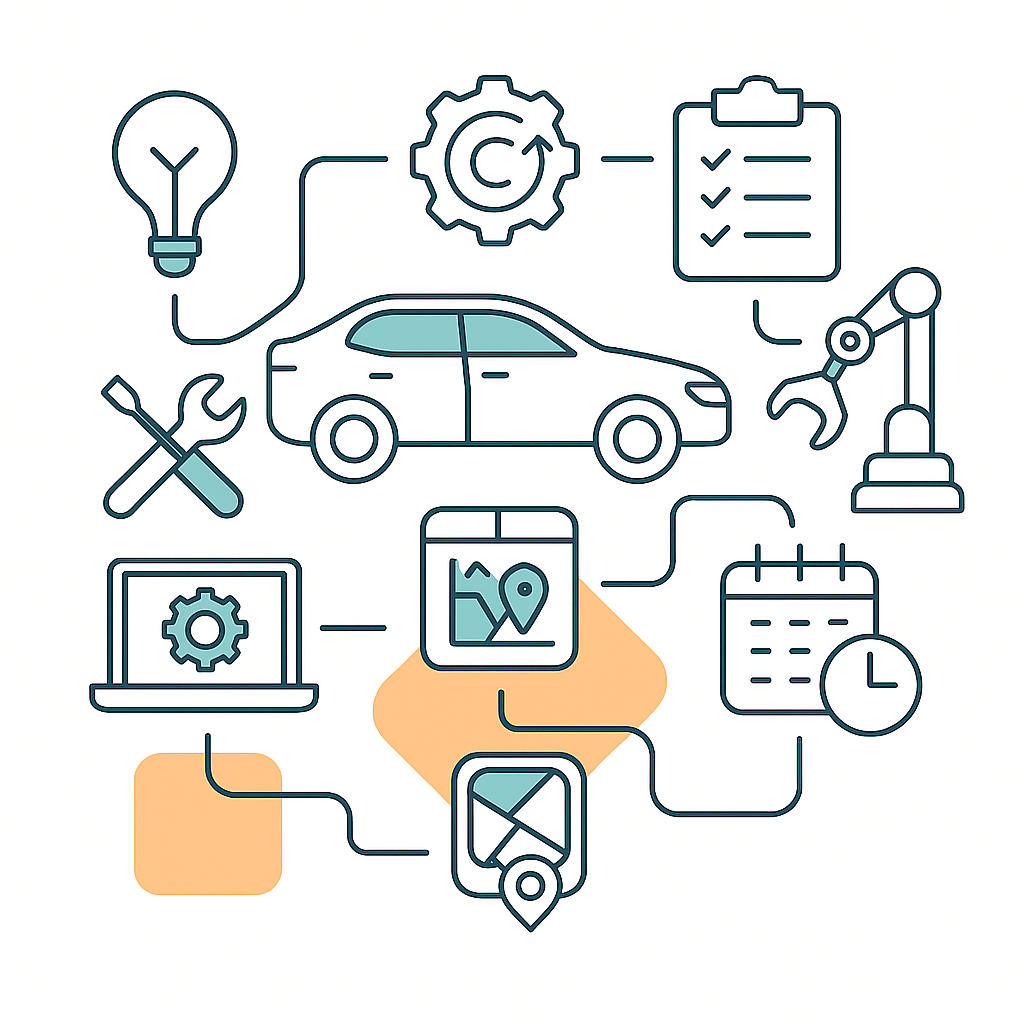
Product Lifecycle Management (PLM) Systems
PLM tools are the backbone of automotive engineering coordination. They manage everything from design specs and part numbers to change requests and supplier collaboration.
- Siemens Teamcenter: Widely adopted for its robust engineering data management and CAD integration. Supports global collaboration across OEMs and suppliers.
- PTC Windchill: Offers end-to-end product development visibility, especially effective for configuration and change management in modular vehicle programs.
Why it matters: These tools ensure every team—from design to procurement—works from the same, always-updated source of truth.
Project Tracking & Workflow Management
Tracking thousands of tasks, issues, and deadlines across functions requires powerful and flexible platforms.
- Dart: An AI-powered platform built for automotive-grade project visibility, helping teams streamline cross-functional workflows, track key deliverables, and stay aligned on milestone progress across complex programs.
- Jira: Commonly used in software and Agile development for EV and infotainment teams, where quick iteration and sprint tracking are critical.
- Confluence: Used alongside Jira for documentation, decision logs, and collaborative planning.
Why it matters: These tools help PMs manage both hardware timelines and software sprints - often on parallel tracks.
Simulation & Virtual Testing Platforms
Modern vehicle programs reduce costly physical prototypes by relying on advanced simulation environments.
- Dassault Systèmes (CATIA, SIMULIA): Used for CAD design, structural analysis, and real-time virtual validation.
- Ansys: Popular for thermal, electronic, and safety simulations, especially in EV battery and ADAS development.
Why it matters: Simulation tools accelerate development while maintaining compliance with performance and safety benchmarks.
Communication & Collaboration Platforms
In large, globally distributed teams, real-time communication is essential for speed and alignment.
- Slack: Enables fast, topic-based collaboration between design, engineering, and supply chain teams.
- Microsoft Teams: Widely used by traditional OEMs for secure video calls, file sharing, and integrations with other MS Office tools.
- Digital Dashboards: Custom tools that provide real-time visibility into program status, KPIs, and cross-team dependencies.
Why it matters: Clear communication is the foundation of cross-functional project execution, and these tools keep everyone connected.
Lead With Systems That Keep Speed and Scale in Sync
In the fast-paced world of automotive innovation, managing complexity isn’t optional - it’s the standard. From hybrid methodologies and lean execution to tech-driven planning and real-time collaboration, the automotive industry shows what’s possible when strategy meets structure.
If your projects demand speed without sacrificing quality, it’s time to rethink your systems. Apply these proven approaches to lead with clarity, scale with confidence, and deliver with precision, no matter your industry.